生产现场成本改善实战全记录
在汽车制造领域,丰田公司2019年新车型量产过程中实施的成本改善项目,为行业提供了设备优化与流程再造的经典范本。项目团队通过三阶段改善方案,成功将单品生产成本降低6.3%,日均利润增长260元。
指标类型 | 改善前数据 | 改善后数据 | 变化幅度 |
---|---|---|---|
设备综合效率(OEE) | 72% | 89% | +23.6% |
单件生产成本 | 7.99元 | 6.42元 | -19.6% |
日均可动时间 | 20.4H | 22.8H | +11.8% |
项目背景与挑战
新车型导入初期,350T成型机组面临三大核心难题:模具切换耗时超出标准值24%、材料损耗率超标1.8个百分点、设备综合效率低于行业基准值15%。这些问题导致单件生产成本逼近售价红线,项目利润率仅为1.7%。
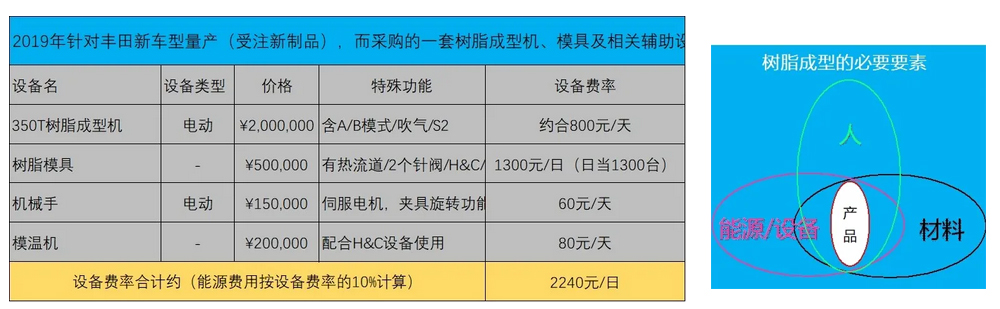
成本优化实施路径
设备效能提升方案:
- 合模速度参数优化:将锁模压力从320Bar提升至350Bar
- 模具冷却系统改造:循环水温度降低8℃
- 机械手取件轨迹优化:单次取件时间缩短3秒
材料成本控制措施:
- 原料预干燥工艺改进:含水率控制在0.12%以下
- 边角料回收系统升级:材料利用率提高2.3%
- 色母粒自动配比系统:配色误差率降低至0.8‰
改善成果与效益分析
通过12周持续改进,项目组达成关键指标突破:单件生产周期从62秒压缩至42秒,模具切换时间减少38%,设备综合效率提升至93%。财务数据显示,单日净利润增加260元,年度经济效益预估可达62万元。
成本构成 | 初始成本 | 优化后成本 | 降本幅度 |
---|---|---|---|
设备费率 | 2.2元 | 1.72元 | 21.8% |
材料消耗 | 4.4元 | 4.0元 | 9.1% |
质量损失 | 0.35元 | 0.12元 | 65.7% |
持续改善机制建设
建立三级成本监控体系:产线级每小时数据采集、车间级每日成本核算、工厂级每周效益分析。实施改善提案制度,累计收到员工建议127条,其中38项进入实施阶段,预计可带来年度附加效益15万元。