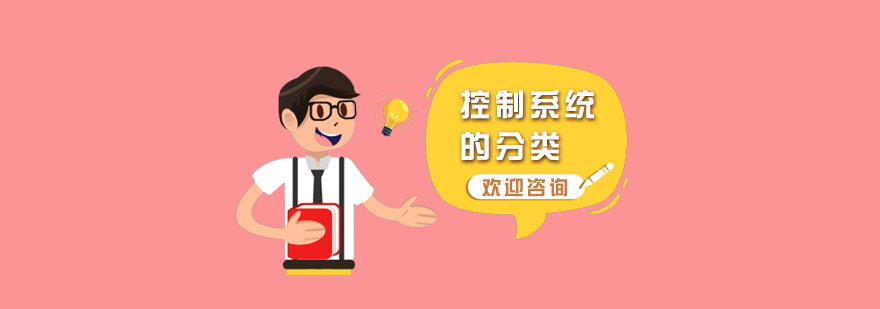
在工业自动化领域,机器人控制系统的架构设计直接影响设备运行效率。当前主流控制系统主要呈现三种典型架构,每种架构在实时响应、扩展能力等方面存在显著差异。
控制系统架构对比分析
控制类型 | 处理器架构 | 实时性表现 | 扩展能力 | 典型应用场景 |
---|---|---|---|---|
主从控制 | 双处理器架构 | 毫秒级响应 | 模块化扩展 | 精密装配作业 |
分散控制 | 多处理器网络 | 微秒级响应 | 分布式扩展 | 复杂产线协同 |
集中控制 | 单处理器架构 | 秒级响应 | 有限扩展 | 基础教学设备 |
主从控制架构技术解析
双处理器架构将管理功能与运动控制分离,主处理器负责坐标变换和轨迹规划,从处理器专注关节运动控制。这种架构在汽车焊接生产线中表现突出,能实现0.1mm级别的定位精度,但模块间的通信延迟可能影响多轴协同效率。
分散式控制系统优势
多处理器网络架构允许各控制模块独立运作,通过工业以太网实现数据同步。某电子设备制造商采用该方案后,产线调整时间缩短40%,设备利用率提升至92%。但需要特别注意网络拓扑设计,避免数据包冲突导致的控制延迟。
集中控制系统的适用边界
单处理器方案在基础教学机器人中仍占主流,成本较分散系统降低65%。但在处理32轴以上复杂系统时,响应时间会呈指数级增长,这在某大学实验室的对比测试中得到验证:当控制轴数超过24个时,轨迹误差达到警戒阈值。
系统选型决策要点
- ▶ 精度需求:微米级作业首选主从架构
- ▶ 扩展预期:未来可能增容优先考虑分散式
- ▶ 预算限制:成本敏感场景可评估集中方案